OFFSHORE CONCRETING- A Case Study RE-GASIFICATION TERMINAL (RGT) SUNGAI UDANG, MELAKA, MALAYSIA
- Benjamin Chandran
- Aug 12, 2021
- 2 min read
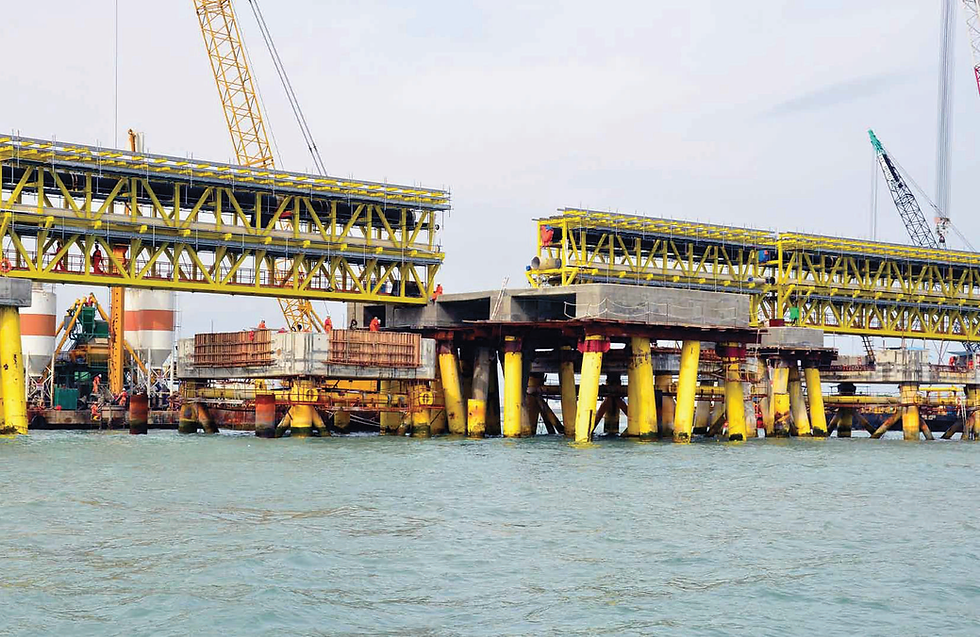
OFFSHORE CONCRETING
- A Case Study
RE-GASIFICATION TERMINAL (RGT) SUNGAI UDANG, MELAKA, MALAYSIA
PETRONAS’ plan for the development of the project, also referred to as Re-gasification Terminal (RGT) Sungai Udang, was officially announced on 10 June 2010.

The project was then estimated to cost US$945 million. Following the announcement, the task of developing the RGT was assigned by PETRONAS to PGB, which implemented the project on a fast-track basis to meet its completion deadline in record time and with a significantly lower cost than its original budget.

Situated 3 km offshore Sungai Udang, Melaka, the RGT is considered an engineering feat by the industry.

Developed based on a revolutionary design, it comprises the world’s first-of-its-kind re-gasification unit on an island jetty (JRU), two floating storage units (FSU) and a three-km sub-sea pipeline connecting to a new 30-km onshore pipeline that links to PGB’s existing Peninsular Gas Utilisation (PGU) pipeline network.

With LNG shortages and subsidisation providing new challenges, Petronas decided to build a new state-of-the-art offshore facility incorporating a world-first jetty regasification unit.

Situated 8 km off the coast of Melaka, the Sungai Udang regasification terminal accommodates super tankers, a necessity as local supply is depleted and the need for imported gas becomes a reality.

The terminal is 980 metres long and has annual capacity of 3.8 million tons, with two floating storage units permanently berthed at the jetty to receive and store LNG.
The island jetty and processing units transport regasified LNG by subsea pipeline to the Peninsula Gas Utilisation pipeline network.
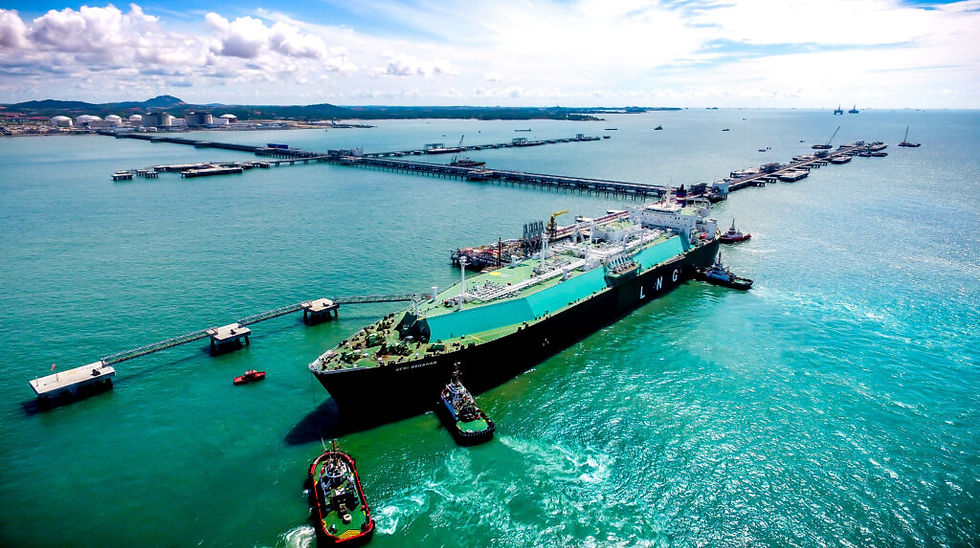
Completed in July 2012, the terminal’s innovative design enabled it to be built within a 1 billion ringgit budget, instead of the originally estimated 3 billion. Being located offshore also saved two years of construction time.
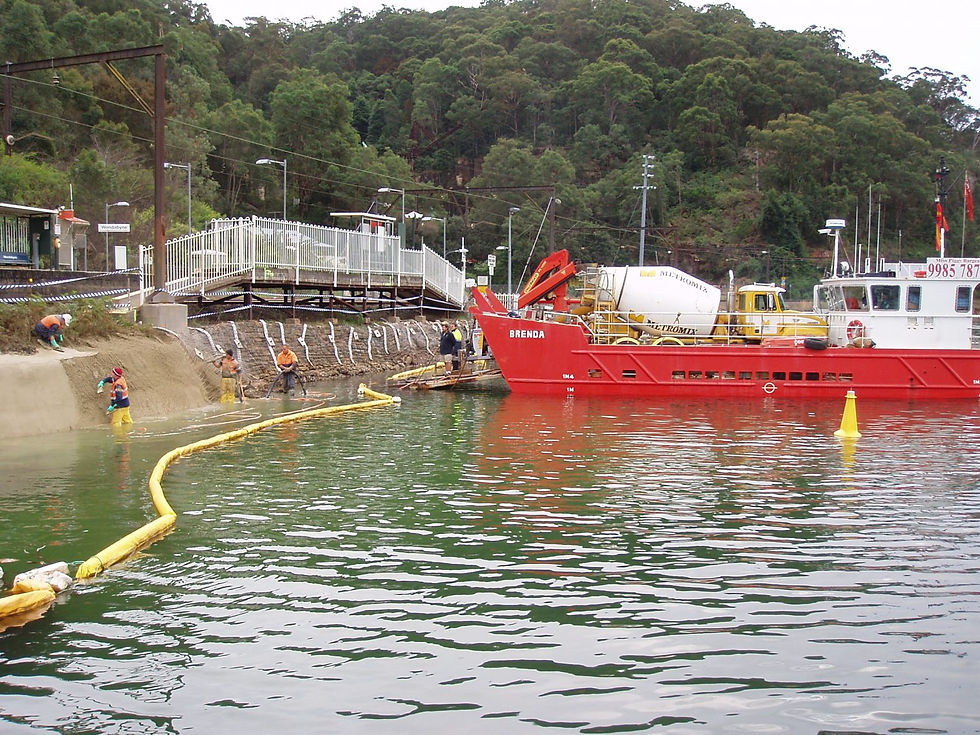
THE CHALLENGE
As an offshore construction project, the biggest challenge was logistical.

The supplier needed to ensure concrete and cement were readily available on site, round the clock. Being situated 8 kilometres offshore, simply reaching the site posed challenges.

SOLUTION:
‐ Accurate and efficient project management and logistics to ensure optimal consistency in the supply of the floating plants.
‐ Sophisticated logistical planning and production mapping, which was necessary due to limited road infrastructure, festive season road closures, and weather disruption in the interior of Melaka, hindering the access of cement trucks.
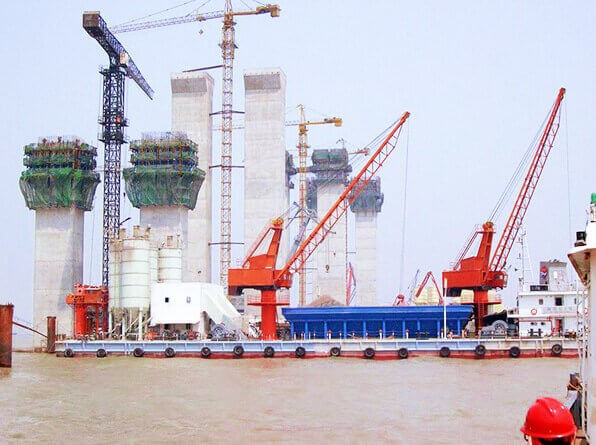
This demonstrates the importance of a great partner – able to deliver where others simply could not.
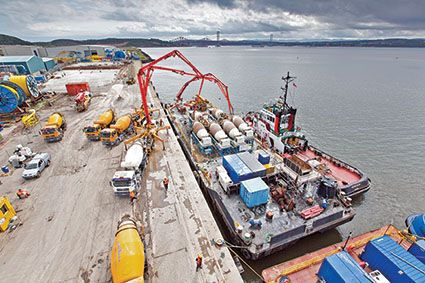
A team that went to extraordinary lengths to understand and accommodate the needs.
Chat with a concrete engineer today about your project:
Comments