HIGH STRENGH CONCRETE - Aggregates Selection and Handling
- Robert Albert Jeyaretnam
- Aug 22, 2021
- 1 min read

In high-strength concrete, careful attention must be given to aggregate size, shape, surface texture, mineralogy, and cleanness.

For each source of aggregate and concrete strength level there is an optimum-size aggregate that will yield the most compressive strength per unit of cement.
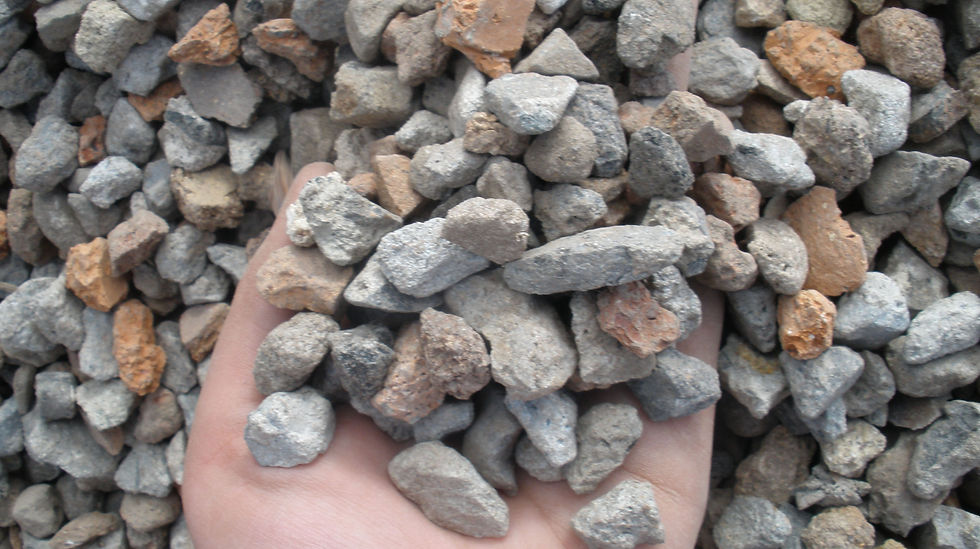
To find the optimum size, trial batches should be made with 19 mm (3⁄4 in.) and smaller coarse aggregates and varying cement contents.

Many studies have found that 9.5 mm to 12.5 mm (3⁄8 in. to 1⁄2 in.) nominal maximum-size aggregates give optimum strength.

In high-strength concretes, the strength of the aggregate itself and the bond or adhesion between the paste and aggregate become important factors.
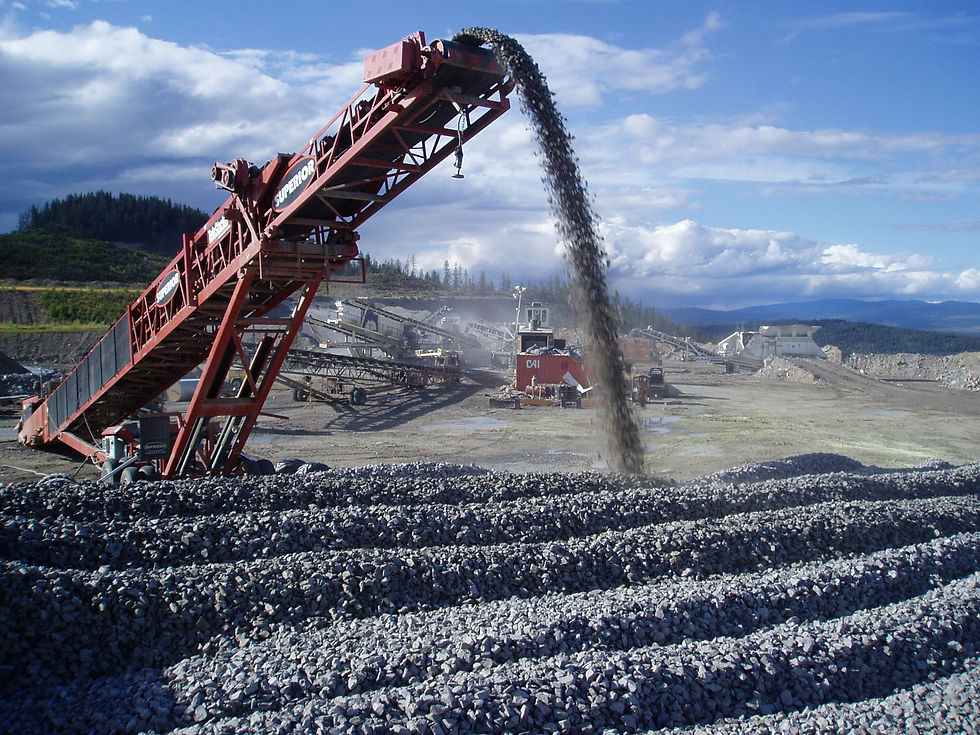
Tests have shown that crushed-stone aggregates produce higher compressive strength in concrete than gravel aggregate using the same size aggregate and the same cementing materials content; this is probably due to a superior aggregate-to-paste bond when using rough, angular, crushed material.

For specified concrete strengths of 70 MPa (10,000 psi) or higher, the potential of the aggregates to meet design requirements must be established prior to use.

Coarse aggregates used in high-strength concrete should be clean, that is, free from detrimental coatings of dust and clay. Removing dust is important since it may affect the quantity of fines and consequently the water demand of a concrete mix. Clay may affect the aggregate-paste bond.


Washing of coarse aggregates may be necessary.

Combining single sizes of aggregate to produce the required grading is recommended for close control and reduced variability in the concrete.
Chat with a concrete engineer today about your project:
Comments