CONCRETE MIX DESIGN
- Ir Wan Kadir Wan Ahmad
- Aug 8, 2021
- 3 min read

Concrete mix design is the mixture of materials that make concrete. The materials are cement, stone aggregate, sand and water. When mixed producing concrete.

The cement, when mixed with water, creates a paste that coats the sand and aggregate. The water causes the cement to hydrate, and a chemical reaction takes place.
The ratio of the materials determines the strength of the concrete.
CONCRETE MIX DESIGN AND STRENGTH CLASSIFICATIONS
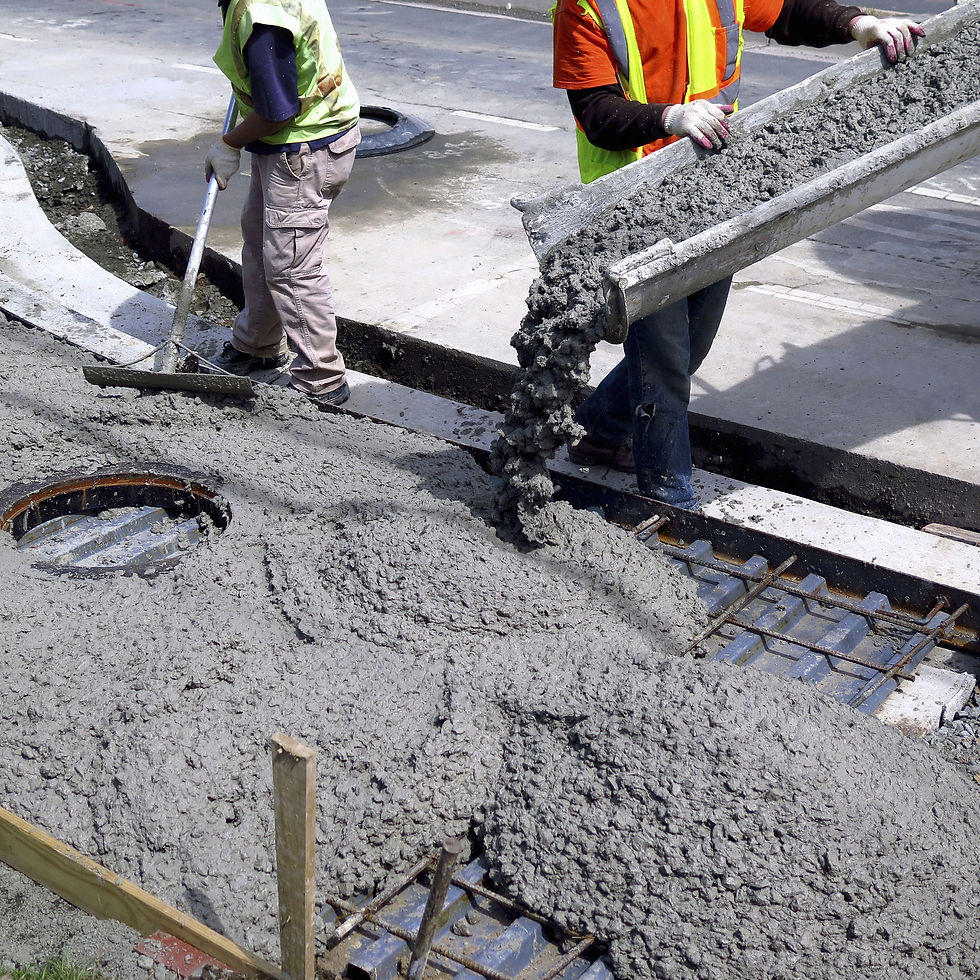
The list below gives the strength classification and concrete mix design. The “M” represents Mix, and the number represents the strength in N/mm2 after 28 days. For example, the M40 grade will reach a strength of 30 N/mm2 after 30 days from the initial set.
The initial set is when the concrete becomes a solid mass. The intitial setting time can vary from an hour to a number of hours. This is important as some concrete may need to be pumped, spread or finished. If the concrete set too quickly, it can be costly to take out.
GRADES OF CONCRETE –CONCRETE MIX DESIGN
(Cement: Sand: Aggregate)
M5 1:5:10
M7.5 1:4:8
M10 1:3:6
M15 1:2:4
M20 1:1.5:3
M25 1:1:2
M30 1:0.75:1.5
M35 1:0.5:1
M40 1:0.25:0.5
CONCRETE MIX DESIGN AND WEIGHT CONVERSION
The table below gives you the concrete mix designs and converts them into kg to make 1m3 of concrete.

PRESCRIBED CONCRETE MIXES
A prescribed concrete is a mix where the purchaser prescribes the exact mix. The mixes are normally designed by a professional concrete technician.
The mixes below are for a guide only as each mix is designed for a specific purpose.
When designing a concrete mix, you should always consider the required strength, durability, and workability of the concrete for it’s purpose.
Manufacturing concrete using this method is a good guide but too much cement is used.
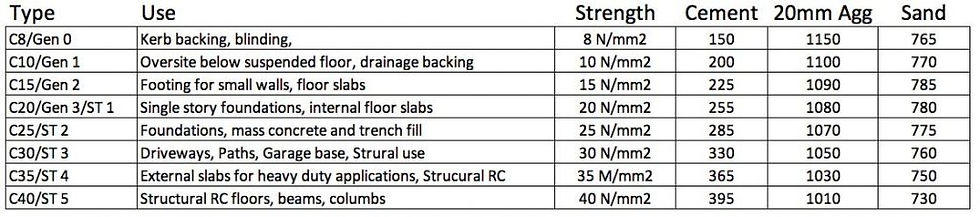
Water Content and Concrete Mix Design
The more water that is added to a concrete mix, the more fluid and workable the concrete becomes. However, this comes with a price of strength. More water equals weaker concrete.
The water-cement ratio is important for the concrete to reach its design strength. This is why it is essential to order concrete that has been designed for a particular slump. Adding water onsite to improve workability will weaken the concrete and can cause failure.

The slump measures the workability. A 25mm slump is a stiff mix, whereas a 150mm slump is more workable and flowing.
TESTING CONCRETE MIX DESIGN
The design strength of concrete is the strength after 30 days of curing. Concrete normally reaches 50% of its design strength after 7 days and 75% after 21 days.

Concrete is normally tested at 7 days and 30 days.
The 7 days test will give an idea of the full strength of the concrete. The 30-day test will give the actual strength of the concrete.
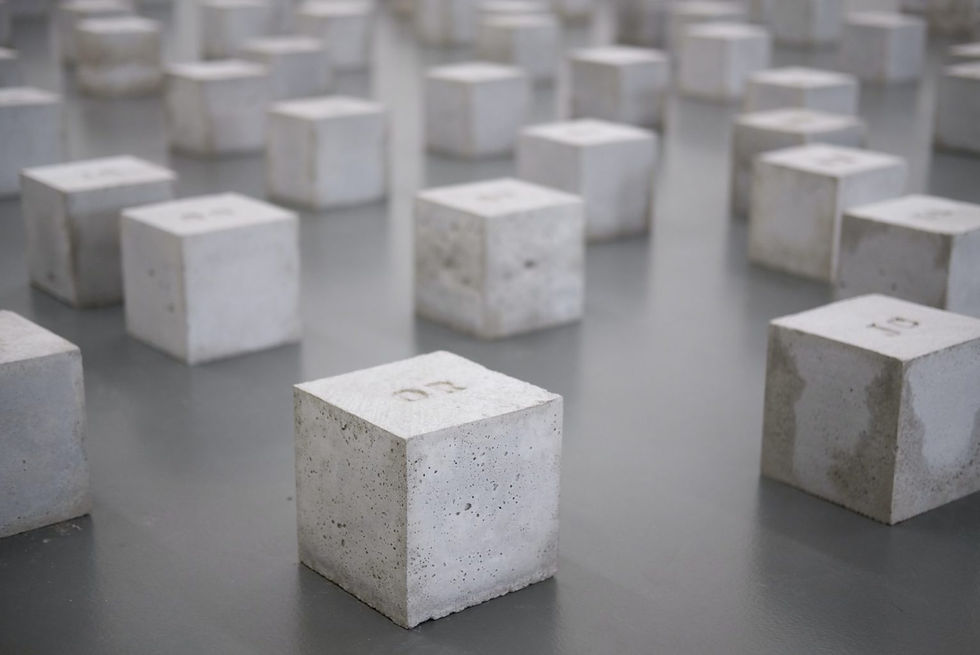
Concrete is tested by making a concrete cube. Cube size is normally 150mm x 150mm x 150mm in size.
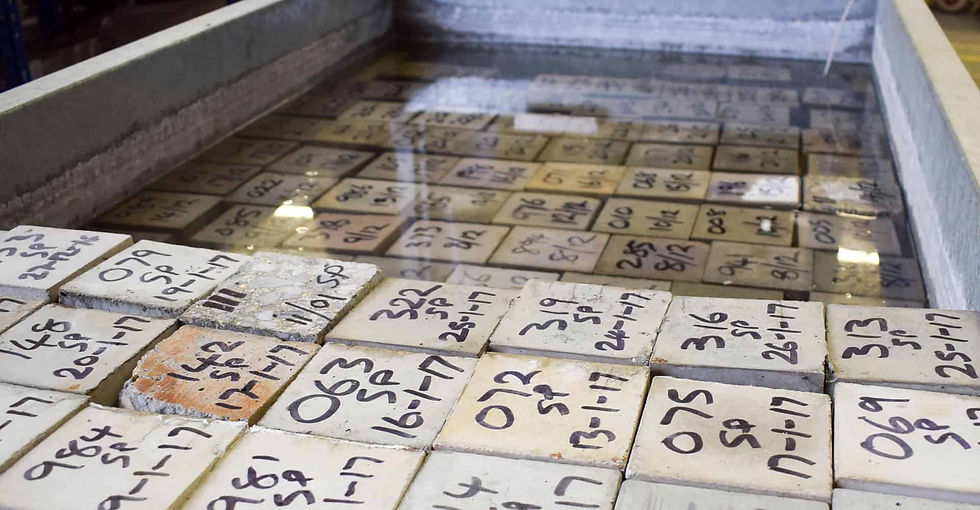
The cube is put in a curing tank that has a temperature of 20 degrees centigrade after one day to cure.

To test the concrete the cube is crushed using a concrete cube testing machine.
CONCRETE MIX DESIGN AND ADMIXTURES
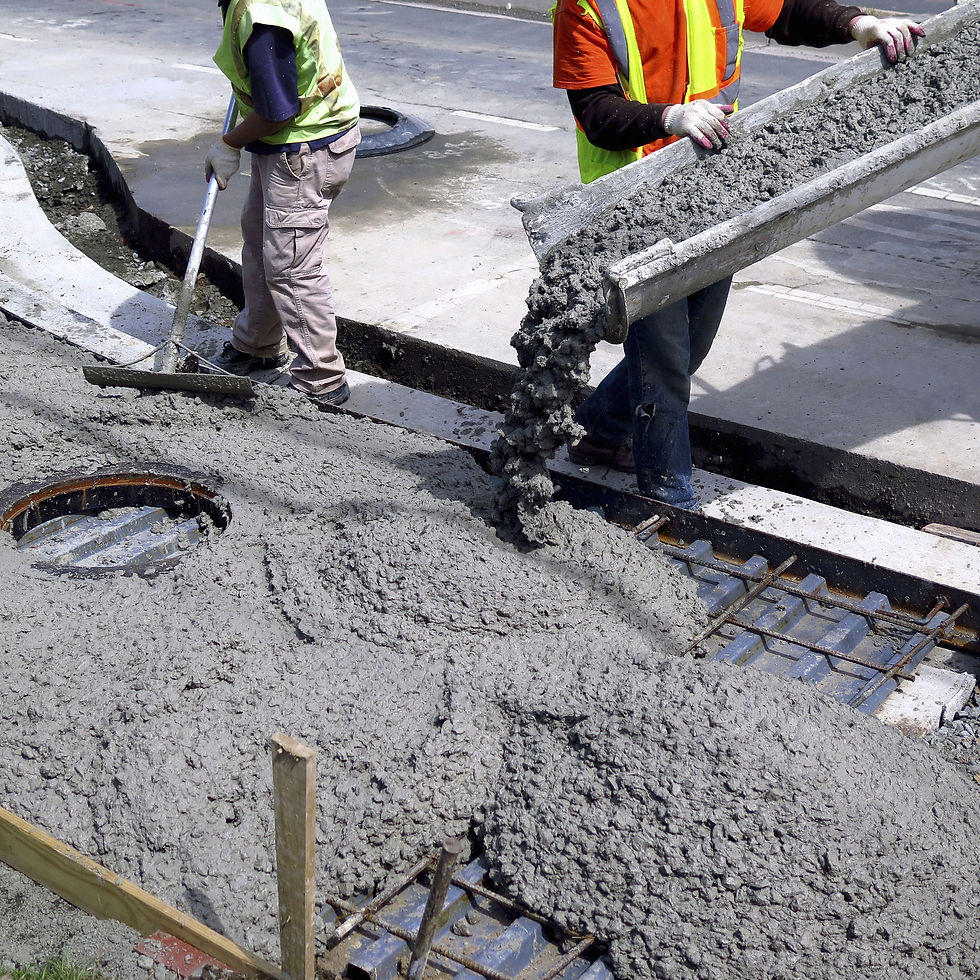
Concrete admixtures can adjust many characteristics of concrete for example:
• Water reducing concrete admixtures
• Superplasticising concrete admixtures
• Set Retarding concrete admixtures
• Accelerating concrete admixtures
• Air-entraining concrete admixtures
• Water Resisting concrete admixtures
• Retarded, ready-to-use Mortars
• Sprayed Concrete admixtures
• Corrosion inhibiting concrete admixtures
• Foamed Concrete admixtures
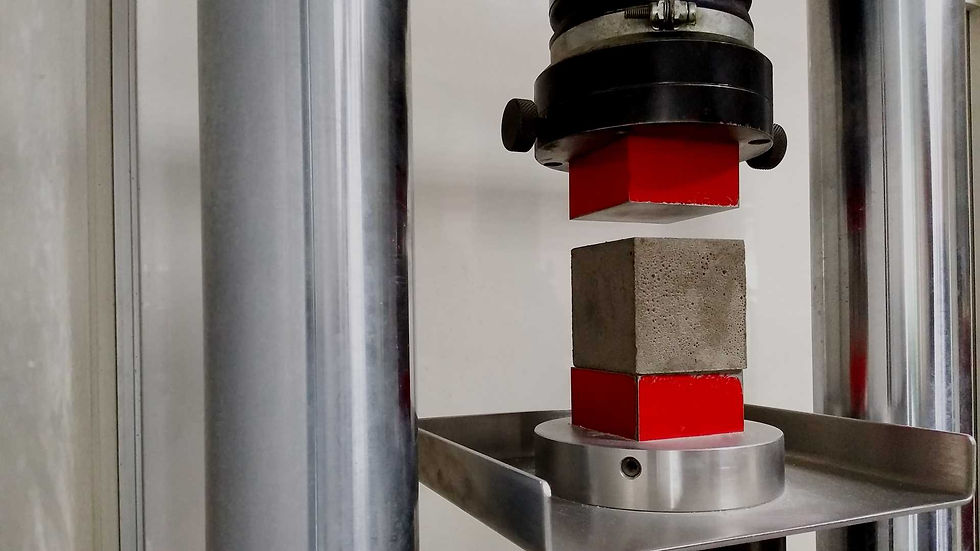
Concrete Mix Design and British Standards
The British Standard for concrete design is BS 8500.
The standard is in two parts. Part one deals with specification and part two deals with materials.
The European standard is EN 206
Chat with a concrete engineer today about your project:
https://wa.me/60195136630
https://myconcreteengineer.wixsite.com/malaysia
https://www.linkedin.com/company/concrete-engineers-malaysia
https://www.facebook.com/concreteengineersmalaysia
https://www.facebook.com/concreteengineersmalaysia
https://twitter.com/ConcreteEnginee
Comments